Anti-Foam Control Solutions-- Reliable Foam Management for Industrial Applications
Anti-Foam Control Solutions-- Reliable Foam Management for Industrial Applications
Blog Article
Exploring Different Kinds of Anti-Foam Control Solutions for Various Industries
The monitoring of foam in industrial procedures is a critical aspect that can affect both product quality and operational effectiveness across different sectors. Different industries, such as food and drink, drugs, and wastewater treatment, face one-of-a-kind challenges associated to foam formation, necessitating customized anti-foam services.
Comprehending Foam Development
Foam development is a complex physical sensation that takes place when gas is caught within a fluid, creating a steady framework of bubbles. This procedure is influenced by different factors, consisting of the buildings of the liquid, the nature of the gas, and outside problems such as temperature level and pressure (Anti-Foam Control Solutions). The stability of foam is greatly determined by the surface stress of the viscosity and the liquid, as these residential or commercial properties dictate exactly how conveniently bubbles can form and persist
In numerous industrial applications, foam is an unwanted by-product that can impede procedures, lower effectiveness, and effect item top quality. The development of foam is often intensified by anxiety, blending, or chemical responses, bring about raised functional challenges. Understanding the systems behind foam formation is crucial for establishing efficient control methods.
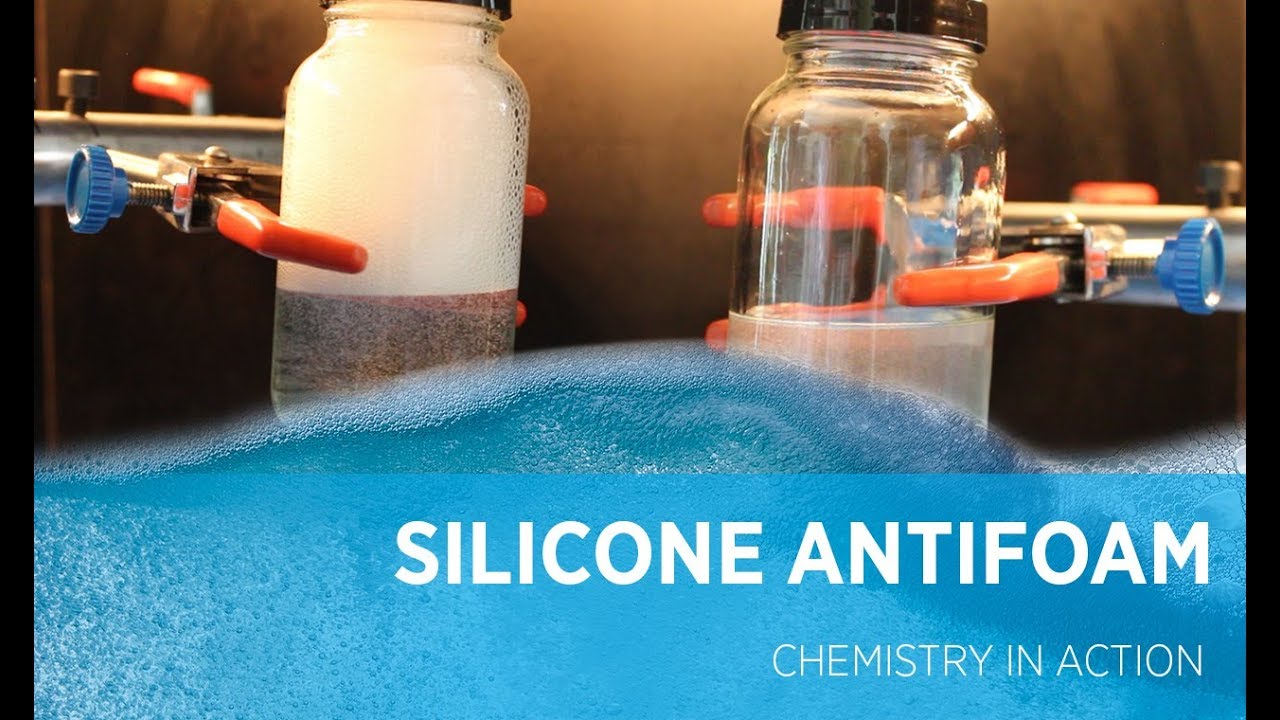
Types of Anti-Foam Brokers
Various types of anti-foam representatives are used across markets to battle the challenges presented by foam development. These agents can be extensively classified into two primary kinds: silicone-based and non-silicone-based anti-foam representatives.
Silicone-based anti-foam agents are very efficient as a result of their distinct buildings. They contain polydimethylsiloxane (PDMS) and can considerably lower surface area tension, permitting fast foam collapse. Their security at high temperature levels and in various pH atmospheres makes them appropriate for varied applications, consisting of production and chemical handling.
On the various other hand, non-silicone-based anti-foam representatives consist of organic compounds such as fatty acids, esters, and waxes. They typically work by providing a physical barrier that interrupts foam development.
Furthermore, some anti-foam agents integrate both silicone and non-silicone parts to enhance efficiency across particular problems. Recognizing the unique characteristics and applications of these anti-foam representatives is crucial for choosing the appropriate service for foam control difficulties in numerous industrial setups.
Applications in Food and Drink
In the food and beverage industry, efficient foam control is paramount to making sure product high quality and process effectiveness. Too much foam can result in operational difficulties, such as tools overflows, reduced processing capability, and incongruities in item texture. Various applications within this industry, consisting of developing, milk handling, and juice production, demand customized anti-foam options to resolve specific foaming problems.
For circumstances, in brewing, foam stability is important for both the top quality of the beer and the performance of the brewing process. Anti-foam agents are employed to minimize undesirable foam throughout fermentation and product packaging, ensuring a smoother workflow and maintaining desired flavors. In a similar way, in dairy processing, the production of products like yogurt and cheese requires careful foam management to avoid splilling and keep appearance.
In juice production, foam can obstruct purification procedures, impacting yield and clarity. Here, the application of appropriate anti-foaming representatives can maximize production prices and boost product appearance - Anti-Foam Control Solutions. On the whole, picking the ideal anti-foam control options tailored to the one-of-a-kind needs of each application is necessary for preserving quality and efficiency in the food and drink market
Solutions for Pharmaceuticals
Reliable monitoring of foam generation is essential in the pharmaceutical market, where precision and pureness are extremely important. Foam can interfere with different processes, consisting of blending, filtering, and sanitation, possibly compromising product top quality and efficacy. The choice of suitable anti-foam remedies is necessary to preserve functional performance and regulatory conformity.
Silicone-based anti-foam agents are extensively used as a result of their effectiveness and compatibility with a variety of pharmaceutical solutions. These representatives function by minimizing surface area tension, therefore destabilizing the foam framework. Furthermore, non-silicone choices, such as fatty acids and natural oils, are getting traction for their eco-friendliness and biodegradability, lining up with industry trends towards sustainable techniques.
It is vital to consider the details application when selecting an anti-foam option, as the formula should not detrimentally impact the energetic ingredients or the end product. Moreover, compatibility with cleansing and sterilization processes is essential to make certain that the anti-foam agents do not useful reference present pollutants. Constant surveillance and screening of foam control measures can improve efficiency, making certain that pharmaceutical processes continue to be compliant and optimal with strict sector standards.
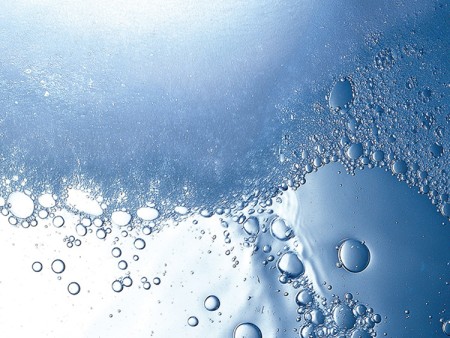
Wastewater Treatment Approaches
As markets increasingly concentrate on sustainability, carrying out reliable wastewater treatment strategies has actually ended up being important for reducing environmental impacts. Wastewater treatment is a critical process that makes sure the safe disposal or reuse of commercial results, hence minimizing air pollution and saving water sources.
One primary method includes using organic treatment techniques, such as turned on sludge processes, which make use of bacteria to break down natural impurities. This method is commonly complemented by click for source sophisticated filtration and sanitation techniques, making certain the effluent meets regulatory requirements.
Furthermore, chemical therapy options, such as coagulation and flocculation, are employed to get rid of suspended solids and liquified materials. The assimilation of anti-foam agents is crucial in this context, as foam can hinder treatment effectiveness and make complex stages of clarification and separation.
In addition, membrane modern technologies, consisting of reverse osmosis, are gaining traction from this source because of their ability to generate high-grade effluent suitable for reuse in various applications. Overall, a combination of these strategies customized to certain market requirements can considerably improve the efficiency of wastewater treatment, adding to an extra lasting future.
Verdict
Reliable foam control is vital throughout numerous markets to enhance item quality and process efficiency. The selection of appropriate anti-foam agents, whether green or silicone-based non-silicone options, plays a crucial function in attending to specific foaming difficulties encountered in food and beverage processing, drugs, and wastewater treatment - Anti-Foam Control Solutions. Proceeded exploration of diverse anti-foam options will certainly promote better operational outcomes while making sure ecological conformity and source healing, thereby adding to sustainable techniques within these sectors
Various industries, such as food and drink, pharmaceuticals, and wastewater therapy, face unique obstacles associated to foam development, requiring tailored anti-foam services. Different applications within this industry, including brewing, dairy products processing, and juice production, demand tailored anti-foam solutions to address certain foaming problems.
Anti-foam representatives are used to minimize unwanted foam during fermentation and product packaging, making sure a smoother operations and keeping desired tastes. These agents work by decreasing surface area stress, thus destabilizing the foam framework. The selection of suitable anti-foam representatives, whether silicone-based or environmentally friendly non-silicone alternatives, plays an important function in addressing particular frothing challenges run into in food and beverage handling, pharmaceuticals, and wastewater therapy.
Report this page